The University of Texas at Austin has experienced extensive growth, from 18,774,098 square feet in 2008, to 24,934,833 square feet in 2023, resulting in increased campus energy consumption. To counter the impact of this increase, UEM invested in a series of optimization technologies that are instrumental not only in mitigating the energy increase, but also in bringing down consumption levels.
Power Plant Megawatt Management System
The Power Plant Megawatt Management System is a supervisory control system with logic that calculates the megawatt set-points for the combustion turbine generator (CTG) and for steam turbine generators (STGs) in order to keep the amount of power purchased from the utility equal to the value entered by the operator in the most economical manner. For example, the management system will try to load the CTGs to their maximum so that the amount of steam produced by the heat recovery steam generator is maximized. Likewise, the logic determines the amount of power for the STGs based on their current extraction flows. It should be noted that when an STG is on, there is a minimum condenser flow that must be maintained. The load control logic will only calculate set-points for the pieces of equipment that are in auto mode.
Read the article: Electrical Control and Energy Management System of a University (PDF).
Chilling Station Optimization
District Cooling
Cooling energy at The University of Texas at Austin (UT Austin) is provided by an extensive district cooling system, using large and efficient machines aptly called “chillers.” Each of the university’s 18 main campus chillers can cool the equivalent of 10,000 average Texas homes. These machines operate in chilling stations strategically placed throughout campus, pumping the heat energy from the chilled water loop, through the chillers’ refrigerant, and finally to condenser water that is cooled by evaporation in cooling towers. The chilled water is pumped throughout campus to each building through a massive network of insulated piping, most of which is located under the campus streets and sidewalks in over nine miles of underground tunnels. With the hundreds of campus chilled water customers and hundreds of motors of varying age and efficiency working simultaneously to keep the Texas heat outdoors, UEM at UT Austin continuously challenges the industry status quo by modeling and optimizing the chilled water system live in real-time with sophisticated software to ensure the utmost efficiency and reliability.
Thermal Energy Storage
In similar fashion to the state power grid, the university’s electrical demand rises and falls with the Texas heat. Hot and humid outdoor conditions require the district cooling system to ramp up output, increasing electrical demand accordingly. Daytime building occupancy further increases this daytime demand, all while the university’s main campus generation capacity remains fixed. As the campus continues to grow, electrical demand follows suit, and among its arsenal of tools the university utilizes thermal energy storage (TES) to help equalize this highly-cyclical demand. Two large chilled water storage tanks totaling 9.5 million gallons--one located behind Creekside Residence Hall and the other at the northwest corner of Red River and Martin Luther King, Jr. Blvd.--store cold water that is chilled at night when electrical demand is low and pumped to buildings for use during the day when electrical demand is high. These TES tanks offset the need for new generation capacity, saving the university precious space and construction costs of more than $150 million.
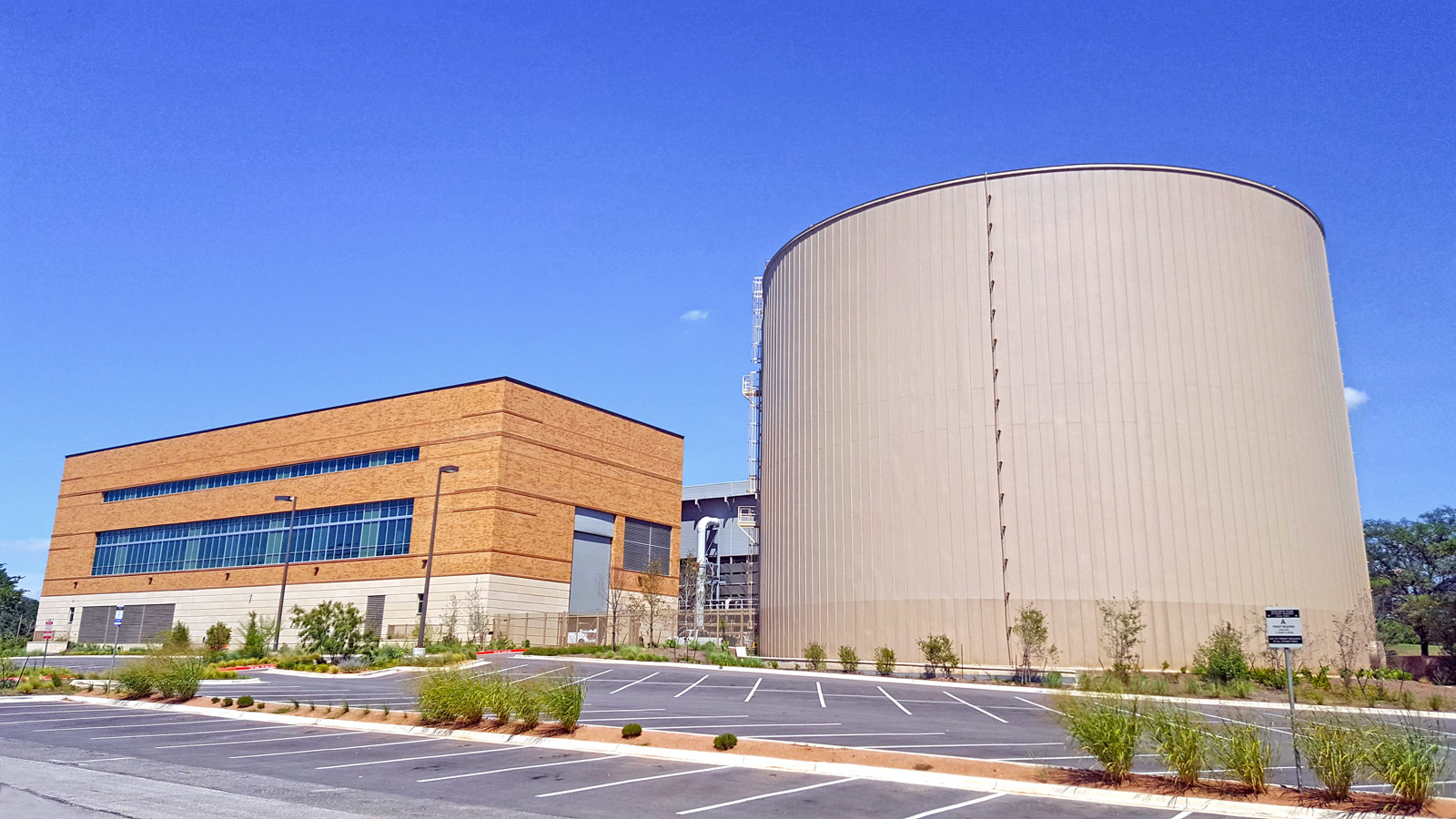
TERMIS
TERMIS is a real-time modeling system that continuously compares a sophisticated computational model of the campus’ district cooling networks piping and other various components against hundreds of live data points. Any significant variance between the model and live data counterpart is represented graphically in an intuitive map format to alert engineers and technicians to a potential problem. In this way, the TERMIS system has saved the university millions of dollars in avoided energy costs. Inclusion of historical trends and weather data also allows TERMIS to help UEM forecast campus cooling needs to assist with maintenance and outage planning.
In addition to live modeling and forecasting, TERMIS also allows for the modeling of any manner of “what if” scenarios, such as future construction, chilling system component outages, and potential delivery issues such as a pipe blockage or breakage. This helps assure that the cooling needs of the university are several steps ahead of construction and growth.
Optimum Energy
The university also utilizes an optimization platform called Optimum Energy to control operations of each individual chilling station. Optimum Energy trends the efficiency curves of each plant component at every possible operating condition and then adjusts the operating parameters of each component to provide the most efficient whole-system operation at a rate of once per second. UEM has been able to maintain an average chiller plant efficiency of ~0.6kW per cooling ton. Chilling station (CS) 7 near Dell Medical School is expected to be one of the most efficient plants of its kind in the world. The resultant cost savings utilizing Optimum Energy in the chilling stations has already proven tremendous, totaling nearly one million dollars annually.
Plant Health Index
UEM has always supported the tradition of teaching and research excellence at UT Austin and understands the importance of maintaining a high standard of education. To meet this need, UEM adopted an innovative predictive maintenance based solution to help identify equipment failure in advance. This Predictive Analytic Software Solution or Plant Health Index (PHI) helps improve operational excellence by using the early detection feature of the system to capture anomalies in the behaviors of sensors, equipment and the operation of process plant systems. PHI also helps analyze process uncertainty using statistical learning by modeling the operational history in a simple setup.
Learn more about how UT Austin uses Plant Health Index (PDF) for its plant systems.